Project Overview
Project Details
- Duration: October - December 2023
- Team Size: 4
- Role: Responsible Engineer
- Status: Retired
Technical Overview
- Valve Type: Swagelock Needle Valve
- Actuator Type: DC Motor Driven
- Fluid Type: Nitrous Oxide
- Cost: $200
Odyssey was ERPL's throttleable hybrid rocket engine
designed to produce 500 lb of thrust using HTPB and
Nitrous Oxide as propellants. To be able to throttle the
engine, a custom valve actuator was created by using
ODrive DC motors to turn the main oxidizer needle valve
throughout the burn.
While throttling was successful, the engine did
not survive the hotfire due to unrelated issues and the
project was cancelled shortly after in pursuit of liquid
rocket development.
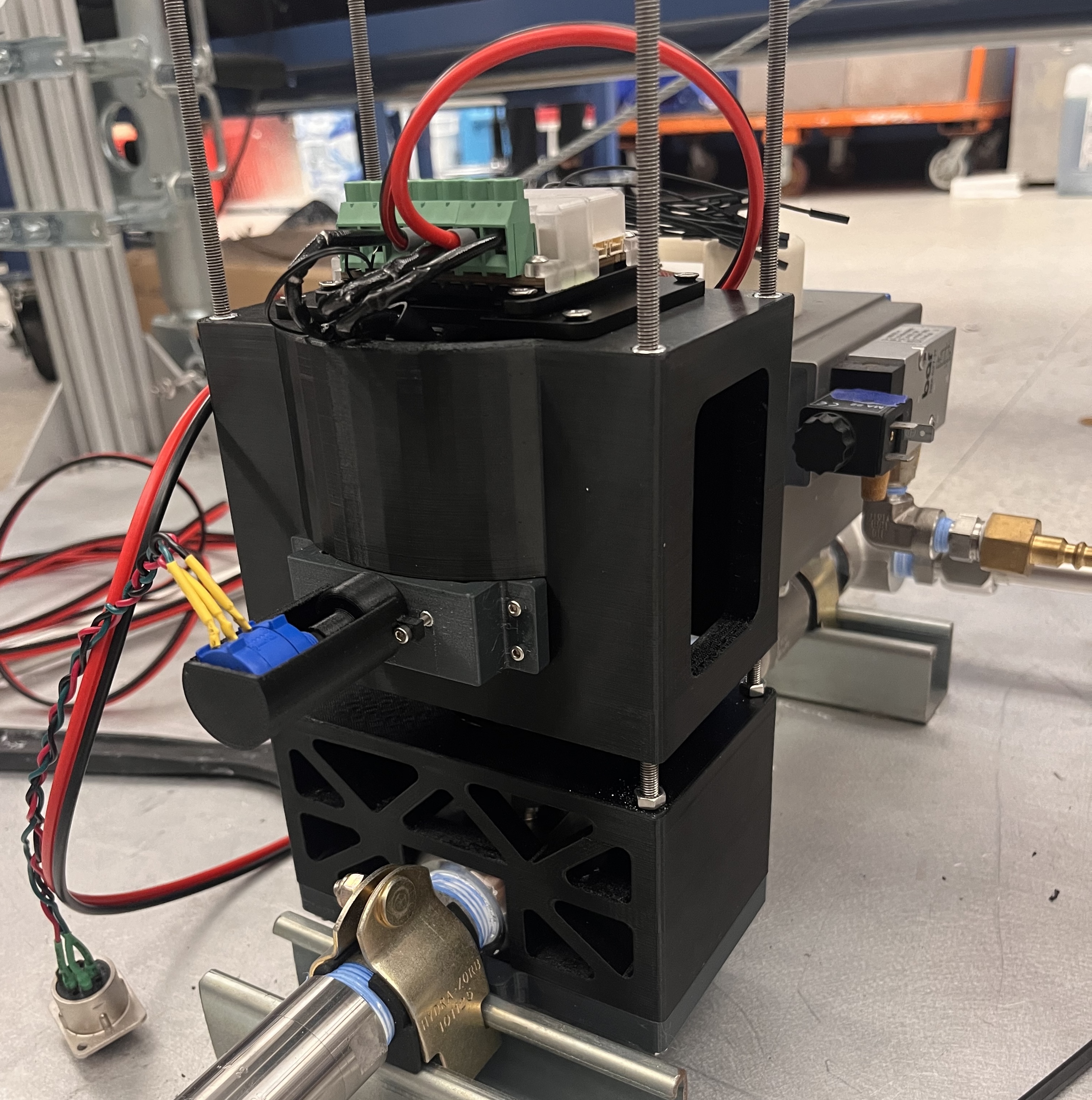
Final design of the throttle valve actuator implemented into the oxidizer feed line.
Design & Development Process
Requirements
The throttle valve actuator needed to be able to hit variable valve positions very quickly to meet the throttle profile. Additionally, it had to be low cost and integrate with the existing needle valve.
Conceptual Design
The design concept was to direct drive the stem of the needle valve using a DC motor. For postional redundancy, a potentiometer would also be positioned in connection with a gear system to provide positional verification at all times.
Manufacturing
Most of the casings and structural supports were 3D printed for simplicity. However, the coupler connecting the motor to the needle valve was CNCed out of aluminum using a PocketNC.
Testing & Validation
On top of countless dry runs and checkouts, the actuators were used in a system-level waterflow to help determine the change in oxidizer flow rate in relation to the valve position.
Challenges & Solutions
Challenge 1
Valve stem height changes with rotation
Solution:
Changed design to allow the entire upper chassis to move with the stem as it screws in and out of the valve body.
Challenge 2
High cracking torque from valve seating
Solution:
Adjusted throttle logic to slow down the last 5% of the seating and full opening positions to prevent the valve from getting stuck in it's position.
Results & Impact
Throttle valve in action during Odyssey Hot Fire #2. Wait to see the nozzle reappear at the end.
Key Achievements
- Developed a throttle valve actuator capable of varying mass flow to the engine
- Gained some useful data from water flow characterization
- Learned a lot about rapid prototyping and design iteration
The throttle valve successfully controlled the mass flow of oxidizer to the hybrid engine, however, the results were unable to be characterized due to a rapid unscheduled disassembly of the engine. We were able to extract a lot of preliminary characterization data from the waterflow that helped us further understand how the throttle valve affected pressure drop across the system and mass flow into the engine. Additionally, the design and manufacturing process from this valve taught me a lot of critical engineering lessons at the beginning of my education.
Lessons Learned
This project taught me a lot of rewarding (and sometimes difficult) lessons about fundamental design principles and how to apply rapid prototyping to converge on a design.
Technical Insights
- • Principles of fluid mechanics and control systems
- • Designing for different manufacturing techniques
- • How to iterate quickly through designs
Process Improvements
- • Streamlined data analysis & system integration
- • Fault tolerance and system safing
- • Troubleshooting anomalies
Future Work & Next Steps
This project was deprecated after we shifted toward designing a liquid-capable test stand, however, these principles could eventually be applied to a bi-propellant feed system.